Saku Metall Allhanke Tehases töötab automaatladu nimega "nighttrain", mis on ühendatud stantspinkidega. Nimi tuleneb sellest, et tootmine on võimeline töötama ka inimese sekkumiseta, selgitas ettevõtte juhataja Rain Johanson möödunud nädalal Pärnu Tarneahelakonverentsil.
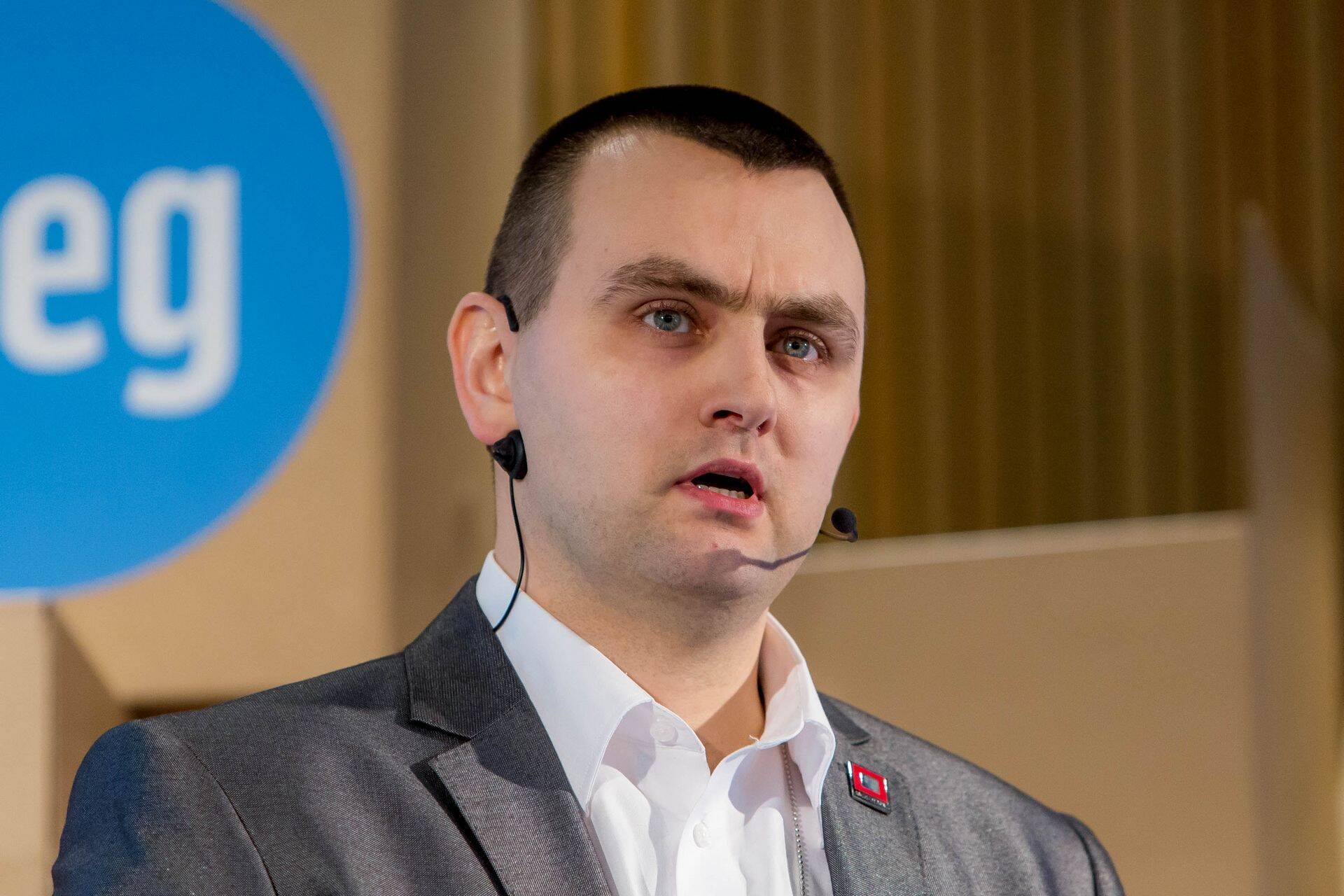
- Rain Johanson Foto: Urmas Kamdron
Saku Metall Allhanke Tehas ASi juhataja Rain Johanson esines möödunud nädalal toimunud Pärnu Tarneahelakonverentsi „Midagi on puudu“ teisel päeval ja kõneles sellest, kuidas on ettevõte 2004. aastast pidevalt arenenud ja milliseid probleeme on sel teekonnal ette tulnud. Johanson tegi ülevaate sellest, kuidas töötab 2015. aastal kasutusele võetud automaatladu.
"Ettevõte arenes ja pidevalt soetati juurde uusi masinaid. Masinate paigaldus toimis layout´i, mitte tootmisvoo keskselt. Iga uue pingi korral vaadati ekraanil küll tehase layout´i ja otsiti koht, kus oli piisavalt ruumi, kuid asukoha mõistlikkust tootmisvoo loogilisuse seisukohast ei hinnatud,“ selgitas Johanson ettekande sissejuhatuses.
Ta lisas, et pärast 2008. aastat valmis ettevõttel juba kolmas tootmishall ja siis oli tootmisvoog juba nn päris peapeale pööratud. Segadust külvas ka 2012. aastal valminud neljas hall koos värviliiniga.
Johansoni sõnul oli 2014. aastaks selge, et nõnda enam töö jätkuda ei saa ja olukorrale on vaja leida väljapääs. "Meie eesmärk on alati olnud tehnoloogia arenguga kaasas käia ja pidevalt pingiparki uuendada. Lahendust nägime automaatse lehelao soetamises," jätkas Johanson ja lisas, et ühtlasi tõstsid nad tehase sisseseade 8000 ruutmeetri ulatuses ümber.
Tootmispinda raisati
"Juba automaatlao ehitamise ajal selgus, et olime aastaid tehase tootmispinda raisanud, sest ehituse ajaks tühjaks tehtud esimene hall ei halvanud ümbertõstetud tehase tööd kuidagi. Lao valmides 2015. aastal muutus tootmisvoog aga taas loogiliseks," avas Johanson uue lao mõjusid.
Ta selgitas, et uus tootmisliin toimib nii, et tõstukiga tõstetakse toormaterjal pakkidena kassetile, mis viiakse laos toimetava rongiga riiuli juurde. Laoga on ühendatud kaks stantspinki, mis vastavalt tootmisplaanile tellivad kasseti õige materjaliga stantspingi kõrvale. Pärast töötlust viiakse väljalöödud detaili toorikud tagasi lattu. Ladu toimib puhvertsoonina.
"Põhimõtteliselt on meil täna valmidus, et tootmisliini ühest otsast pannakse pakk toormaterjali lattu ja tootmisliini teisest otsast saame painutatud detaili kätte nii, et vahepealsetes operatsioonides ei ole inimkäsi seda puudutanud," ütles ta.
Positiivsed mõjud kohe näha
Automaatlao esimesed positiivsed mõjud olid kohe pärast paigaldamist näha. Näiteks hoiti juba tublisti ruumi kokku, sest 300-ruutmeetrisele pinnale paigaldati 1500 ruutmeetrit riiulipinda. Samal ajal tähendanuks ladustamine endisel viisil kümme korda suuremat põrandapinda. Lao kandevõime on tuhat tonni.
Teine mõju oli praak, mis tekkis toormaterjali käsitsemisest. Praak oli võimalik nüüd elimineerida. „Kuni nn automaatlao ajastuni komplekteerisime enne stantsimisse viimist erinevad lehtmaterjalid ühele alusele kokku käsitsi. Seetõttu tekkis materjalile tihti kriimustusi ja pinnadefekte,“ selgitas Johanson ja lisas, et nüüd toimub materjali kassettide vahetus töötluse ajal ja selliseks eelkomplekteerimiseks vajadus puudub. „Samuti toimub detailide mahalaadimine pingist manipulaatorite abil – manipulaatorid suudavad käsitleda ka suuri detaile neid kahjustamata.“
Kolmas mõju on tööjõukulud, sest ettevõte ei vajanud enam niipalju töötajaid. Pingi varustamine ja toodangu mahalaadimine ei vaja Johansoni sõnul enam tõstukit. Lisaks ei vaja pooltoodangu liigutamine stantsimisest puhvrisse ja puhvrist painutusse enam logistikuid, sest see kõik toimib automaatselt.
„Efektiivsemaks muutus ka tootmise varustamine. Tootmisplaani järgi saab lattu valmis panna suurema koguse materjali. Toormaterjali liikumine pinki ja pingist painutusse on nüüd põhioperatsioonide paralleeltegevused ning seetõttu on abiajad nüüd lühemad,“ jätkas Johanson. „Vaatamata eelpool mainitud personali vähendamisele, oleme tänaseks suutnud tõsta tootlikkust automaatlao eelse perioodiga võrreldes üle 50%.“
Töötab inimese sekkumiseta
Tehases kutsutakse automaatladu nightrain´iks. „See tuleneb sellest, et tootmine on võimeline töötama inimese sekkumiseta iseseisvalt. Põhimõtteliselt on tegemist pimetehase lahendusega,“ jätkas Rain Johanson.
Ehkki positiivseid mõjusid oli märgata kohe alguses, selgus lao käivitamisel, et tegelikud väljakutsed on alles ees. „Juurutusprotsess oli keerulisem ja pikem kui eales varem,“ sõnas ta ja lisas, et innovatsiooni lõiv on see, et saad pooleldi, mitte lõpuni arendatud toote. „Saime küll homse päeva, aga pidime oma arendusega selleni ise jõudma. Peamised takistused tekkisid infoliikumisega süsteemis.“
„Selleks, et üldse aru saada, kaardistasime süsteemi infovood ja hakkasime järjest testima. Pärast poole aasta pikkust testperioodi olime läbi käinud terve süsteemi. Tähistasime rohelisega need andmeedastused, mis toimisid, ja punasega need, mis ei toiminid. Aastatepikkuse arendustöö tulemusel jõudsime olukorrani, kus enamik nooli said roheliseks,“ selgitas ta. „Ülejäänud punaste osas loobusime, sest andmeedastus nendes lõikudes osutus liiga aeglaseks ja süsteemi toimivuse mõttes ei pidanud me seda ka vajalikuks.“
Järgmised väljakutsed olid Johansoni sõnul seotud laosüsteemi integreerimisel ettevõtte targa tehase lahendustega. „Me võime lugeda digitaliseerimise alguseks 2014. aastat, sest lisaks tootevoo optimeerimisele hakkasime looma süsteemi, mis toetaks meie tootmise jälgitavust infotehnoloogiliste vahenditega,“ märkis Johanson. „Me ei rahuldunud enam olukorraga, kus üksiku tootmistellimuse tootmisetapi selgitamiseks tuli see tootmisest visuaalselt üles otsida. Hakkasime juurutama online-jälgitavust.“
Tööle saadi automaatsed kulukanded
„Iga ettevõte on kokku pandud klotsidest – masinad, programmid ja erinevad süsteemi täiedavad tarkvarad. Need klotsid ei ole ühesugused – ei suuruselt ega ühilduvuselt,“ jätkas Johanson.
Siinkohal on hea näide Saku Metall ise. „Meil on mitmeid programme projekteerimiseks ja eraldi CAM-tarkvarad masinate programmeerimiseks. Kuna aegade jooksul on soetatud erinevate firmade seadmeid, siis kõigiga käib kaasas oma tarkvara. Lisaks tuleb igal firmal välja uusi tehnoloogiaid ja tarkvarasid, mis eelmise põlvkonnaga ei ühildu,“ kirjeldas tehase juhataja.
„Uue süsteemiga saime andmebaasi, mis oli katushalduseks ühele osale meie tarkvaradest. Meie ambitsiooniks ja eesmärgiks oli oma targa tehase lahendusse kaasata kogu süsteem,“ selgitas Johanson ja lisas, et suurimad väljakutsed olidki seotud just laosüsteemi haldusega, sest lao ja sellega ühendatud pinkide infosüsteem oli kinnine ja väljundandmete usaldusväärsus madal.
Kõik need raskused õnnestus Johansoni sõnul seljatada alles 2017. aasta suveks. „Suutsime tööle saada automaatsed kulukanded – hetkel, mil stantspink materjali töödeldud saab, läheb tagasiside majandustarkvarasse operatsiooni teostamisest ja materjal jagatakse töötluses olnud tootmistellimuste vahel automaatselt kulusse,“ selgitas ta.
Mis on puudu?
Puudu on automaatlao töökindlusest – laost on saanud tehase süda. „Kõigile on selge, mis saab vereringest, kui süda seiskub. Tihti räägitakse, kuidas robotid aitavad tõsta efektiivsust ja tootlikkust, kuid väga vähe räägitakse sellest, et samad robotid vajavad ka hooldust,“ juhtis Johanson tähelepanu olulisele probleemile.
„Koos meie laoga on selliseid Eestis vaid mõned. Enne lao soetamist puudus Eestis igasugune kompetents sellise tootmisliini põhimõtete toimimisest,“ rääkis Johanson.
„Isegi praegu on probleeme suuremate tõrgete kiires kõrvaldamises. Tõsiste kompetentsete spetsialistide puudus ei ole ainult tootmisettevõtete mure, vaid see mõjutab ka hooldusettevõtteid,“ sõnas ta ja lisas, et Saku Metall ei näegi muud võimalust, kui ise koolitada oma ettevõtte hooldusosakonna töötajaid, et seeläbi riskid lõpuni maandada.
Puudu on ka lao täielik integreeritus majandustarkvaraga ja Johansoni sõnul elab ladu täna nn omas mullis. „Täpselt on kõik teada alates hetkest, mil materjal lattu sisestatakse, ning teadmised lõppevad detailide väljasaatmisega laost. „Edasiarendusi näeme laos kui ostuspetsialisti funktsioonis, kus vastavalt laokannetele tekivad uued ostuvajadused, mis vormistatakse ostutellimuseks tarnijale,“ sõnas ta.
Kokkuvõttes ütles Johanson, et ettevõte on automaatlao kasutuselevõtust õppinud palju. Näiteks seda, et müümise hetkel ei suuda ostja küsida kõikide vajaduste kohta ja müüja ei oska neid ka pakkuda. „Ükskõik kui hästi sa kaardistad, ikka tuleb ette olukordi, mida ei suudagi ette näha,“ märkis Johanson.
Veel soovitas Johanson kuulajatele, et alati tuleb seadmete müüjalt alati küsida, kuidas on tagatud hilisem hooldus. „Kui pikk on reageerimisaeg ja milline on spetsialistide hulk, võrreldes Eestis müüdud pinkide ja masinate kogusega.“
Pärnu Tarneahelakonverents „Midagi on puudu“ toimus 22.-23. märtsil Pärnus.
Seotud lood
Tarneahela valdkonna tegijad on taas kogunenud Pärnusse, sest täna algas kaks päeva kestev Pärnu Tarneahelakonverents, mis kannab tänavu alapealkirja "midagi on puudu".
Meil on puudu ajast, mil mõelda, kuidas luua suuremat lisandväärtust, ütles Sensei juhataja ja logistikaekspert Illimar Paul täna toimuval Pärnu Tarneahelakonverentsil "Midagi on puudu".
Elvas asuva elektroonikatööstuse Enics Group asepresident protsesside arenduse alal Kaur Andresson tõdes Pärnus toimuval tarneahelakonverentsil, et tarneahela juhtimine nende jaoks võtmeküsimus ning suurim probleem on seal kliendiennustuste ebatäpsus.
On palju asju, millest me täna aru ei saa, aga pead ei tohi liiva alla peita, vaid öelda, et siin on meie jaoks võimalused ja neid tuleb uurida, soovitas Stockholm School of Economics Executive Education õppe- ja arendusjuht Peter Myhrström täna toimuval Pärnu Tarneahelakonverentsil.
Alumiinium on 100% taaskasutatav materjal ja taaskasutatud alumiiniumist uute toodete valmistamine nõuab vaid 5% esmase alumiiniumi tootmiseks kulunud energiast. Seetõttu on oluline tagada, et kogu tarbimisjärgne alumiiniumijääk jõuaks tagasi ringlusesse. Ringmajanduse võtmeks on toote elutsükli planeerimine juba joonestuslaual – taaskasutatavatest materjalidest toodete kujundamine, mis kestavad kauem ja mida saab lahti võtta ning taaskasutada.